processing

Processing transactions are completed in separate transactions depending
on the type of transaction. The processing transaction can be one of the
following types:
- Internal
– Transfers from the farm to an internal plant at cost. Cost will
be determined in the period end process.
- Sales
– Sold from farm to an external plant. Revenue is based on the order
price at time of sale with the cost of sales being determined in the
period end process. There is a switch in setup to determine if customers
are charged on a per head or weight basis.
- Intercompany
Sales - The farm is a profit center and sells the animals to
an internal plant.
The Entity must be created
before creating a Processing transaction.
The following procedures are outlined in the Processing transaction
document:
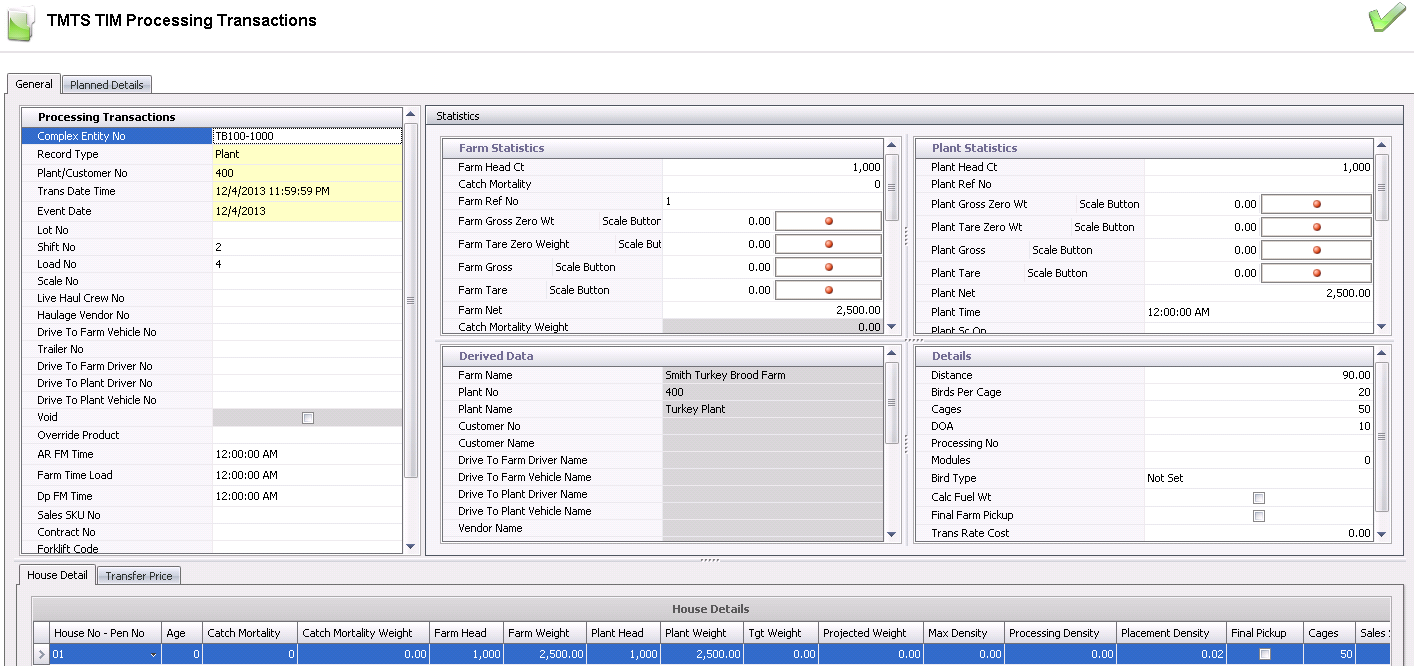
Create
a Processing Transaction
There are several tabs in the processing transaction to record the statistical
processing data for the entity.
- In TMTS>TIM>Transactions,
select Processing.
- In the Processing
Transactions main index, click the
button
to create a new processing transaction.
General
The General tab consists of four sections:
Processing
Transactions
- Click on the Processing Transactions tab.
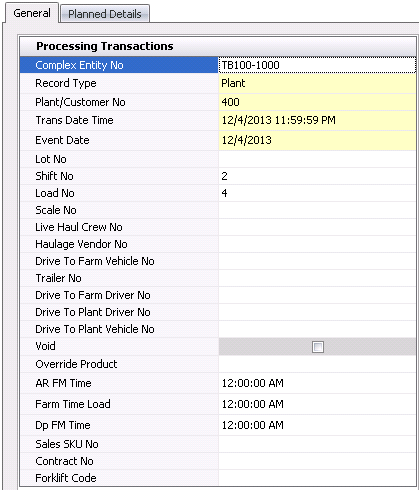
- From the Complex
Entity No drop-down menu, select the farm or entity that is
being processed for the transaction and where the birds are being
delivered from.
Select the Record
Type to determine if the transaction is an internal or external
processing transaction. Available options are Plant or Customer, and
the default is set to Plant.
From Plant/Customer
No, select the plant or customer for the processing transaction.
The available options will default according to the selected record
type.
Trans Date
displays the date of the processing transaction.
Event Date
defaults to the trans date. The date may be changed if the transaction
actually occurred on a different date, however this date does not
affect inventory or accounting.
Lot No
is an optional field to enter a number to identify the processing
transaction.
Shift No
is an optional field to identify the shift receiving the load.
Load No
indicates the load number of the delivery.
Scale
No indicates the scale on which the truck was weighed. Scales
must be defined prior to use in: Admin>Business>General>Definitions>Weight
Scales.
If the transaction
is a plant-type transaction, Live
Haul Crew No can be used to selected a crew that is assigned
to the plant for the processing transaction.
- Haulage Vendor
No can be used to select the haulage vendor, if applicable.
- Drive to Farm
Vehicle No is an optional field to identify the vehicle
used to drive to the farm. Vehicles must be set up prior in:
Admin>Business>General>Definitions>Vehicles.
Trailer No
is an optional field to identify the trailer used to transfer the
product from farm to plant. Trailers must be set up prior in: Admin>Business>General>Definitions>Vehicles.
Drive To Farm
Driver No is an optional field to identify the driver that
drives the truck to the farm. Drivers
must be set up prior in: Admin>Business>General>Definitions>Drivers.
Drive
To Plant Driver No is an optional field to identify the driver
that transfers the product from farm to plant.
Drive
To Plant Vehicle No is an optional field to identify the vehicle
used to transfer the product from farm to plant.
Selecting the Void
flag will cancel the transaction and exclude it from the entity's
statistic.
Override Product
can be used to change the product by selecting the new product from
the drop-down menu. The Override Product options is used when the
entity is placed as one product and processed as another product.
For example, the turkey is
placed in the entity as Broiler Straight Run and then processed as
either Large Straight Run or Small Straight Run. All of the products
need to be set up as Broiler Straight Run, and then any of those products
can be selected using the override option.
In the AR
FM Time field, enter the time that the truck will arrive at
the farm to load the turkeys.
In the Farm
Time Load field, enter the time that the turkeys will be loaded
at the farm.
In the Dp
FM Time field, enter the time that the truck will depart the
farm.
Sales
SKU No is used if the transaction is a customer transaction.
The sales sku must be defined for the order to be created. If there
is a single sales sku assigned to the product, the sales sku will
default, otherwise, the sales sku must be selected.
If the customer
is assigned to a pricing contract, from Contract
No, select the contract that applies to the processing transaction.
From Forklift
Code, select the forklift that is used for the processing transaction.
Statistics
The Statistics section is used to enter the weight and processing details
related to the transaction. *Note:
There is a switch in the system registry that can be used to require the
farm and plant zero weights are entered before the farm and plant gross
weights are entered. The switch is located in: Admin>System>Registry>Poultry
Registry>Plants>Pmts Plant>Protein General>Zero Weight Required.
There are four components in the Statistics section:
Farm
Statistics
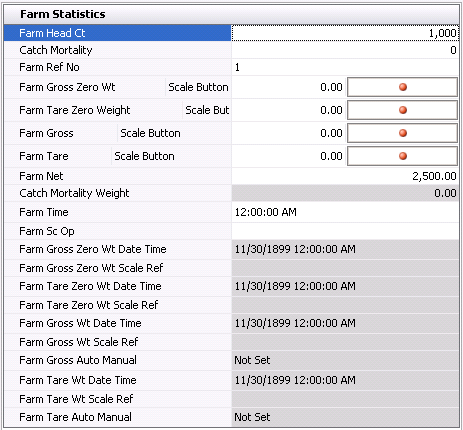
- In the Farm Head
Ct field, enter the number of turkeys that were transferred
from the farm.
- In the Catch
Mortality field, enter the number of turkeys that died during
the round up or gathering of the turkeys to take them to the
processing plant.
- Farm Ref No
is a unique reference number that identifies the transaction at the
farm. This can be manually or automatically entered.
- In the Farm Gross/Scale
Button field, enter the gross weight of the truck at the farm.
- In the Farm Tare/Scale
Button field, enter the tare weight of the truck at the farm.
- In the Farm Net
field enter the net weight of the turkeys at the farm.
- Catch Mortality
Weight will default in from Catch Mortality and displays the
weight of the dead turkeys.
- In the Farm Time
field, enter the time that the vehicle was weighed at the farm.
- Farm Sc Op
(Farm Weight Scale Operator) is used to identify the person who weighed
the turkeys. Scale operators must be set up prior to used in: Admin>Business>General>Definitions>Plant
Scale Operators.
- Farm Gross Zero
Wt Date Time displays the date and time that the gross zero
weight was recorded at the scale.
- Farm Gross Zero
Wt Scale Ref displays the reference number for the gross zero
weight scale reading.
- Farm Tare Zero
Wt Date Time displays the date and time that the tare zero
weight was recorded at the scale.
- Farm Tare Zero
Wt Scale Ref displays the reference number for the tare zero
weight scale reading.
- Farm Gross Wt
Date Time displays the date and time that the gross weight
was recorded at the scale.
- Farm Gross Wt
Scale Ref displays the reference number for the gross weight
scale reading.
- Farm Gross Auto
Manual indicates the gross setting of Auto or Manual.
- Farm Tare Wt
Date Time displays the date and time that the tare weight was
recorded at the scale.
- Farm Tare Wt
Scale Ref displays the reference number for the tare weight
scale reading.
- Tare Auto Manual
indicates the tare setting of Auto or Manual.
Plant
Statistics
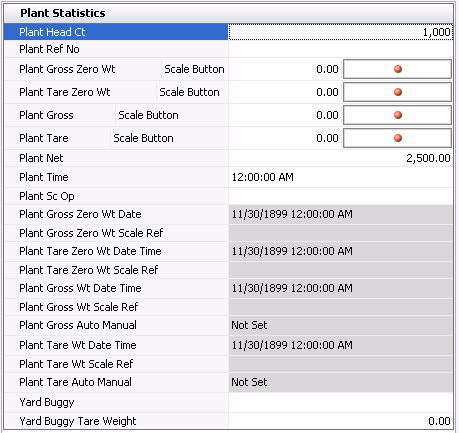
- In the Plant
Head Ct field, enter the number of turkeys that were transferred
from the plant.
- Plant
Ref No is an automatically
generated unique reference number that identifies the plant statistics.
- In the Plant
Gross/Scale Button field, enter the gross weight of the truck
at the plant.
- In the Plant
Tare/Scale Button field, enter the tare weight of the truck
at the plant.
- In the Plant
Net field enter the net weight of the turkeys at the plant.
- In the Plant
Time field, enter the time that the vehicle was weighed at
the plant.
- Plant Sc Op
(Plant Weight Scale Operator) is used to identify the person who weighed
the birds. Scale operators must be set up prior to used in:
- Plant Gross Zero
Wt Date Time displays the date and time that the gross zero
weight was recorded at the scale.
- Plant Gross Zero
Wt Scale Ref displays the reference number for the gross zero
weight scale reading.
- Plant Tare Zero
Wt Date Time displays the date and time that the tare zero
weight was recorded at the scale.
- Plant Tare Zero
Wt Scale Ref displays the reference number for the tare zero
weight scale reading.
- Plant Gross Wt
Date Time displays the date and time that the gross weight
was recorded at the scale.
- Plant Gross Wt
Scale Ref displays the reference number for the gross weight
scale reading.
- Plant Gross Auto
Manual indicates the gross setting of Auto or Manual.
- Plant Tare Wt
Date Time displays the date and time that the tare weight was
recorded at the scale.
- Plant Tare Wt
Scale Ref displays the reference number for the tare weight
scale reading.
- Plant Auto Manual
indicates the tare setting of Auto or Manual.
- From Yard Buggy,
select the yard buggy that moved the trailer loaded with birds around
the yard.
Enter the Yard
Buggy Tare Weight.
Derived
Data
The fields in the Derived Data section default in from the information
entered in the General and Statistics tabs, with no option to modify.
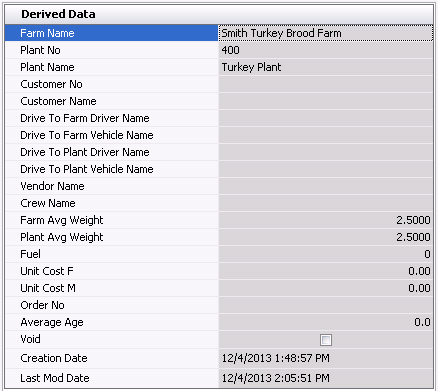
- Farm Name
displays the name of the farm that is being processed/where the turkeys
are being delivered from.
- Plant No
identifies the plant where the turkeys are being processed.
- Plant Name
displays the name of the plant.
- Customer No
identifies the customer, if applicable.
- Customer Name
displays the name of the customer.
- Driver Name
displays the name of the driver delivering the product.
- Vehicle Name
indicates the vehicle used to deliver the product.
- Vendor Name
displays the name of the haulage vendor, if applicable.
- Crew Name
indicates the crew used to deliver the product.
- Farm Avg Weight
indicates the average weight of a single turkey at the farm
- Plant Avg Weight
indicates the average weight of a single turkey at the plant.
- Fuel displays
the total amount of fuel used for the drive.
- Unit Cost F
indicates the average cost per hen.
- Unit Cost M
indicates the average cost per tom.
- Order No
is used if the processing transaction is to an external plant where
turkeys are sold to the plant. When the processing transaction is
created, the Order No field will populate with the sales order number
that is created.
- Average Age
displays the average age of the poults.
- Selecting the Void
flag will cancel the transaction.
- Creation Date
displays the date the transaction was created.
- Last Mod Date
indicates the date the transaction was last modified.
Details
The Details section contains additional details about the birds.
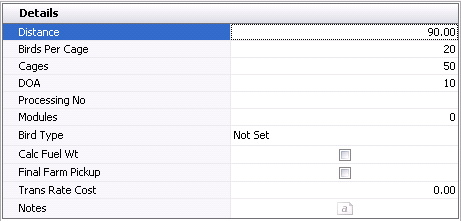
- Distance
is used if the distance to the plant is defined on the farm for the
entity. The distance to and from the plant will be automatically calculated.
- In the Birds
Per Cage field, enter the number of turkeys placed in each
cage for transport.
- Enter the number of Cages
used for transport.
- Enter the number of turkeys that were DOA
(dead on arrival).
- From Processing
No, select the processing type. Processing types must be set
up prior to use in:
- Enter the number of Modules
in the trailer that were filled for transport.
- From Bird Type,
select whether the turkey being processed are Hens or Toms. Bird Type
is a mandatory field as flocks are mixed, but toms and hens are processed
separately.
- Select the Calc
Fuel Wt flag if the total weight will calculate
the fuel-adjusted weight when updating the process receive transaction
weight from the Condemnation transaction.
- Select the Final
Farm Pickup flag if the final pickup for the entity has occurred.
This will mark the entity as 'Sold'.
- In the
Trans Rate Cost field, enter
the transportation rate.
- In the Notes
field, enter any additional information relating to the processing
transaction.
Processing
Details
The Details section contains two components:
House
Details
The House Details contain the processing data for the houses that were
processed in the transaction.
- Select on the House Details tab and click
to
add a new house detail line.

- From House No
- Pen No, select the house or pen number of the farm where
the turkeys are being transferred from.
- Age will
default in based upon the settings that will determine the age of
the entity.
- In the Catch
Mortality field, enter the number of turkeys that died during
the round up or gathering of the turkeys to take them to the
processing plant.
- Catch Mortality
Weight will default in from Catch Mortality and displays the
weight of the dead turkeys.
- In the Farm Head
field, enter the number of turkeys being transferred from the farm.
- In the Farm Weight
field, enter the total weight of turkeys being transferred from the
farm.
- In the Plant
Head field, enter the number of turkeys that arrived at the
plant.
- In the Plant
Weight field, enter the total weight of turkeys that arrived
at the plant.
- In the Tgt Weight
field, enter the target weight for processing.
- Enter the Projected
Weight of the turkeys for processing.
- In the Max Density
field, enter the maximum amount of turkeys/head, as a factor, that
can be processed.
- Processing Density
is a calculated field based on the processing weight and reported
as lbs/ft2 or kgs/m2.
- Placement Density
is a calculated field based on the head placed and reported
as birds/ft2 or birds/m2.
- Select the Final
Pickup flag if this is the last pick-up of the turkeys from
the farm.
- Enter the number of Cages
required for the load.
- Sales SKU No
is used to determine the product being sold, and is set up on the
animal product.
- If the birds are sold on a contract, the Contract No field is used to enter
the contract number.
- Override Product
can be used to change the product by selecting the new product
from the drop-down menu. The Override Product options is used when
the entity is placed as one product and processed as another product.
For example, the bird is placed in the entity as Broiler Straight
Run and then processed as either Large Straight Run or Small Straight
Run. All of the products need to be set up as Broiler Straight Run,
and then any of those products can be selected using the override
option.
Transfer
Price
The fields in the Transfer Price section
will be populated if there are internal prices set up for the product.
These prices are set up in: General>General>Products>Prices>Internal
Prices. A journal will be created based on the internal price.
Period end will reverse and record the actual cost of the bird to the
plant.

- Effective Date
displays the date the transfer price is in effect.
- Product No
indicates the product being transferred.
- Product Name
displays a description of the product.
- Price
displays the total price of the product.
- The Active
flag will be selected by default. De-select the flag if the product
is no longer required.
Planned
Details
If the company is using the LHS (Live Haul Scheduling), the Planned
Details tab will populate from the LHS. In the LHS, the scheduling is
created so that drivers and crews know when to go to each entity, pick
up the birds and deliver them to the processing plant.
The Planned Details tab contains two components:
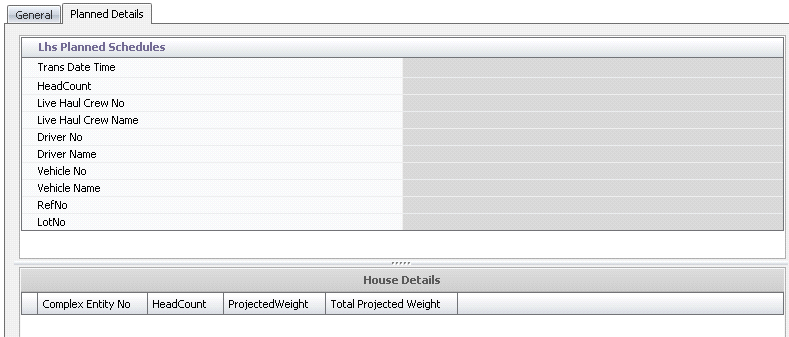
Lhs
Planned Schedules
- Trans Date Time
displays the date and time of the transaction.
- HeadCount
indicates the number of turkeys to be picked up from the LHS.
- Live Haul Crew
No identifies the crew that is picking up the turkeys. Live
Haul Crews must be defined prior to use in: Admin>Business>General>Definitions>Live
Haul Crews.
- Live Haul Crew
Name displays the name of the crew picking up the turkeys.
- Driver No
identifies the driver who is delivering the turkeys.
- Driver Name
displays the name of the driver.
- Vehicle No
indicates the vehicle used to deliver the turkeys.
- Vehicle Name
displays the name of the vehicle.
- Ref No
is a unique reference number used to identify the planned schedule.
The number will be derived from the LHS mode.
- LotN o
contains an optional number to identify the processing transaction.
Planned
House Details
- Complex Entity
No displays the entity that is being processed for the transaction.
- Head Count
indicates the number of turkeys scheduled to be picked up from the
LHS.
- Projected Weight
displays the projected turkey weight.
- Total Projected
Weight displays the total projected weight of all of the turkeys.
Post
a Processing Transaction
Once the processing transaction has been saved and closed, it will need
to be posted. The posting process will lock the transaction from further
edits and post the statistics to the entity. As well, if the processing
transaction is to an external plant, the posting process will automatically
create the sales order and order shipment. For external processing, a
journal transaction will be created to debit the accrued receivable and
credit sales revenue as well as the cost of sales and inventory, only
if an internal price is established.
Journal entries will not be created for internal processing transactions
unless there is an internal price assigned to the product. If that is
the case, there will be a journal transaction created at post where it
will credit the flock value and debit the plant inventory for the internal
prices established for the product. There is a switch in setup to determine
if the product is priced based on a $/head or a $/lb or kg.
- In the Processing Transactions main index, select
the required transaction, rick-click and select 'Post.' Alternatively,
click the green check mark
in the top menu bar and select 'Post Record(s).'
- To un-post a processing transaction, select the
required transaction and right-click to select 'UnPost'. This
process will set the transaction status to 'Reversed' status, which
allows the transaction to be edited.