feed production

Feed Production transactions can be manually entered or interfaced from
a batching system. The feed production will be valued at global post.
There are different types of feed production transactions. All transactions
are captured in the same Feed Production screen and will be handled depending
on the formula type.
Feed Formula
Production: Creates a production transaction and transfers
feed to finished feed inventory.
Pre-Mix
Production: Creates a production transaction and transfers
the finished product to ingredients inventory. Pre-mix production
transactions take two or more ingredients and combine those ingredients
to create another ingredient.
Processed
Ingredient: Creates a production transaction and transfers
the finished product to ingredients inventory optionally with a shrink
factor applied. An example of this type of transaction would be taking
corn from a received state to a coarse or fine grind.
The Feed Production document contains the following components in the
creation process:
- Creating
a Feed Production Transaction
-
Create
a Feed Production Transaction
- In FMIM>Transactions>Feed
Production, select Feed Production.
In the Feed Production main index, select
to
create a new record.
- In the Feed Production Date dialog box, from the
Trans Date/Time drop-down
menu, select the date and time of the transaction. Time is
only required if the Inventory Date Mode is set to 'Date/Time'.
From the Feed
Mill No drop-down menu, select the required feed mill.
Click 'OK' and the Feed Production screen will
appear for the selected mill and date.
FMIM Feed
Formulas
The Feed Formulas grid is where the feed production quantities are entered.
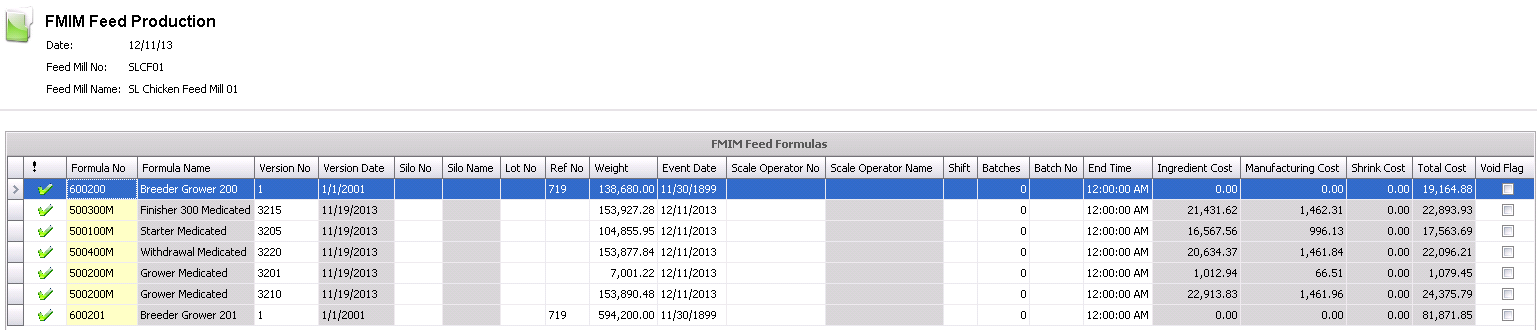
- Select
to
add a new line.
- From the Formula
No drop-down menu, select the required formula from the list
of feed formulas assigned to the feed mill.
- Formula Name
defaults from Formula No and displays a description of the formula.
- Version No
indicates which version is used for the feed production transaction.
The version will default to the most recent version, but can be modified
if required.
- Version Date
is a derived field that indicates the date of the version.
- Silo No
is an optional field to enter the silo in which the feed formula is
being stored. Feed delivery and other transactions will also be tracked
by silo. Costs are also maintained specific to silos
- Silo Name
defaults from Silo No and displays a description of the silo.
- Lot No
is an optional field to enter the lot number if lot number tracking
is used.
- Ref No
is an automatically generated reference number that uniquely identifies
the transaction.
- Weight
indicates the produced quantity.
- Event Date
indicates the date the event occurred.
- From Scale
Operator No, select the required scale operator. Scale
operators must be pre-defined prior to creating a Feed Production
in: .
- Scale Operator
Name defaults from Scale Operator No and displays a description
of the scale operator.
- Shift
indicates the shift that the feed was produced.
- Batches
represents the number of batches that were produced.
- Batch No
is imported from the batching system that references the batch number
of the production transaction.
- End Time
indicates the time that the production run ended.
- The Ingredient
Cost will be $0.00 until the global post process is generated.
Once the global post is run, the total ingredient cost for the production
line will be displayed. The detailed ingredients can be viewed in
the grid to the right.
- If Cost Standards are used, the standard
Manufacturing Cost will be
displayed in this field once global post has been run.
- If Cost Standards are used, the standard
Shrink Cost will be calculated
and displayed in this field after global post has been run.
- Total Cost
represents the total cost of the formula. This amount will not
be defined until the global post process has been run.
- Selecting the Void
Flag will cancel the transaction.
Ingredients
The Ingredients grid indicates the ingredient usage for the selected
formula. Valuation is not completed until global post has been generated.

- In the Ingredient
No field, enter the ingredient that was used.
- Ingredient Name
defaults from Ingredient No and displays a description of the ingredient.
- In the Usage
Amount field, enter the amount of ingredient used for the feed
formula.
- In the Silo
No field, enter the silo that sourced the ingredient if silo
tracking is used.
- Silo Name
defaults from Silo No and displays a description of the silo.
- In the Lot
No field, enter the lot that was used for the formula if lot
number tracking is used. Values will be maintained by lot.
- In the Shrink
Value field, enter the cost of the shrink.
- Usage Value
will initially be zero until global post is run. Valuation is determined
based on inventory costing method – Average Cost or FIFO.
- Usage Unit Value
will initially be zero until global post is run. Valuation is determined
on the inventory unit.
- Theoretical Amount
is the quantity of ingredients that should be used based on the selected
feed formula version
- Theoretical Value
is the value of ingredients that should be used based on the
selected feed formula version.
- Theoretical Variance
Amount is the difference in ingredients required by the feed
formula version as compared to the actual ingredients used, also known
as Mix Variance.
- Theoretical Variance
Value is the difference in value required by the feed formula
version as compared to the actual value used.
Theoretical
(Mix) Variance Value = Version Amount x Standard Value - Actual Amount
x Standard Value
- Standard Amount
is the quantity of ingredients that should be used based on the feed
formula version with the standard flag .
- Standard Value
is the value of ingredients that should be used based on the feed
formula version with the standard flag .
- Standard Variance
Amount is the difference in standard version and feed formula
version used, also known as Reformulation.
- Standard Variance
Value is the difference in standard version values and feed
formula version values.
Standard
(Reformulation) Variance Value = Actual Amount x Standard Value - Standard
Amount x Standard Value